Elevator Pit Waterproofing in San Antonio, TX
At Elevate Enterprises, LLC, we specialize in professional elevator pit waterproofing services throughout San Antonio, TX. Water intrusion can cause significant damage and expensive repairs, but with proper protection, your elevator system remains safe, dry, and reliable.
Our experienced team uses proven techniques and high-quality materials to create long-lasting waterproofing solutions tailored to your specific needs. We don’t believe in one-size-fits-all—every project is approached with precision and care.
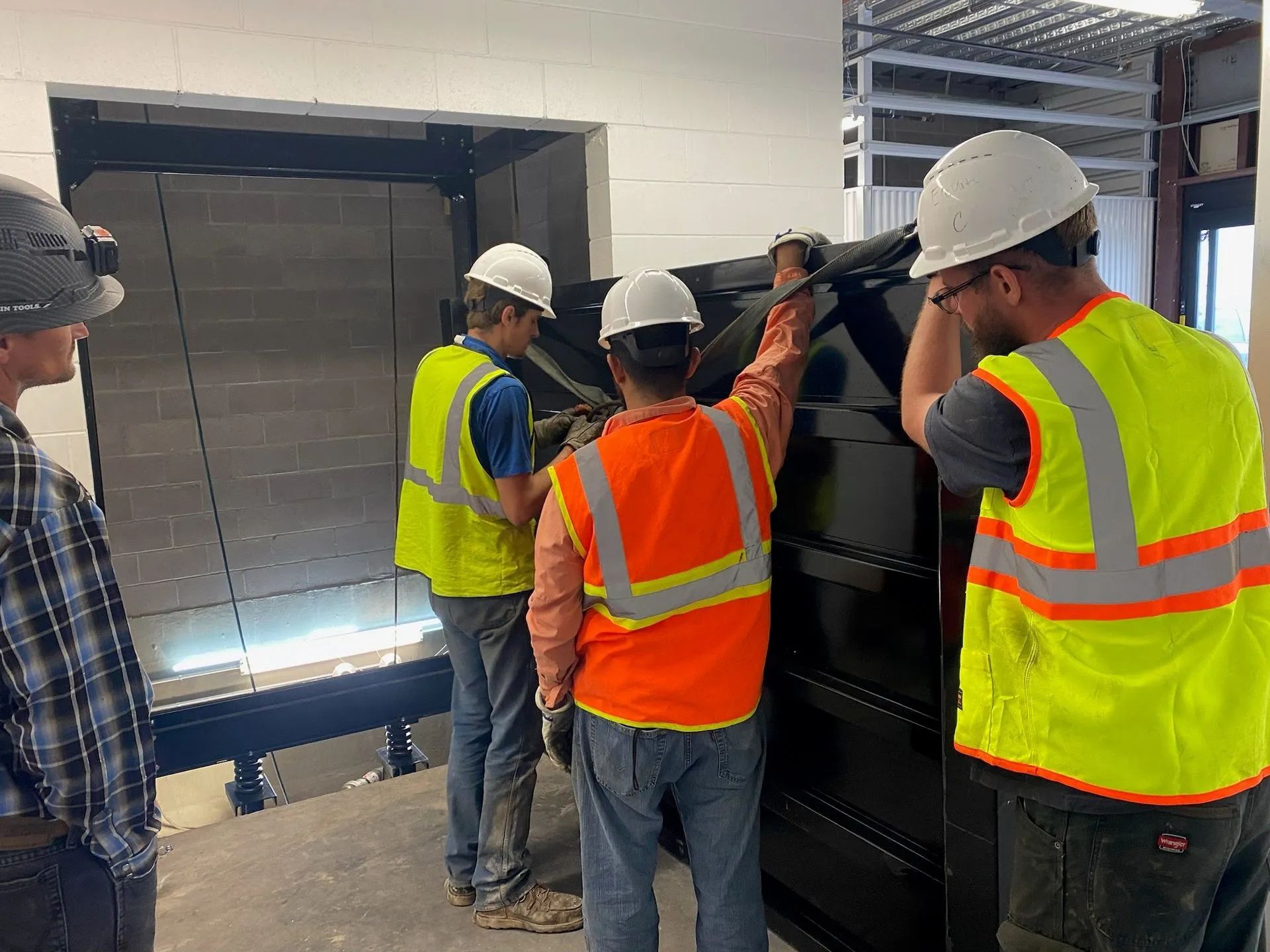
Trusted Waterproofing for Elevator Pits in San Antonio, TX
Why Waterproofing Your Elevator Pit Is Essential
The elevator pit may be out of sight, but it's far too important to be out of mind. As a crucial component of your building's elevator system, it is essential for ensuring everything operates smoothly. Without proper waterproofing, however, the pit is vulnerable to water intrusion—and that can lead to serious problems, including:
Corrosion of Metal Components
Moisture in the elevator pit isn’t harmless—it slowly eats away at key parts of the system. Even a small amount of standing water can cause metal components like guide rails, brackets, and supports to rust over time. As that corrosion builds, it compromises the strength of the structure and leads to more frequent repairs. Waterproofing helps stop the damage before it starts, protecting the system and extending the life of your equipment.
Electrical Hazards and Failures
Moisture and electricity don’t mix—especially in a confined space like an elevator pit. If water gets in, it can seep into wiring, short out controls, or trigger unexpected shutdowns. Even worse, it poses a real safety risk for anyone servicing the equipment. Waterproofing helps ensure that sensitive electrical components stay dry and protected, keeping your elevator system running safely and without surprise malfunctions.
Mold and Mildew Growth
An elevator pit with excess moisture is a breeding ground for mold and mildew. These fungi thrive in dark, damp environments and can quickly spread throughout your building. Not only do they smell unpleasant, but they also degrade indoor air quality and can trigger allergies or respiratory issues in occupants. Preventing moisture intrusion in the pit promotes a healthier environment for all occupants of the building.
Shortened Equipment Lifespan
Elevator systems are built to last—but not if they’re exposed to constant water damage. Over time, moisture can wear down moving parts, corrode internal components, and weaken structural supports. This kind of wear shortens the system’s lifespan, leading to more frequent repairs and early replacement. Pairing waterproofing with ongoing
elevator maintenance and
repair services ensures optimal performance.
Comprehensive Elevator Pit Waterproofing Solutions
At Elevate Enterprises, LLC, we understand the serious impact water damage can have on your elevator system. That’s why we offer complete elevator pit waterproofing solutions designed to protect your investment and keep your building running safely and smoothly.
In-Depth Site Assessment & Inspection
A good waterproofing job starts with knowing exactly what you’re dealing with. We take the time to closely inspect your elevator shaft and pit—checking for signs of moisture, cracks, and any structural concerns. We don’t just do a surface-level look; we get to the root of the problem. That way, we can build a solution that’s tailored to your building and stops issues before they get worse.
Custom-Designed Waterproofing Solutions
One-size-fits-all just doesn’t cut it when it comes to waterproofing. Every building—and every elevator pit—has its own challenges. That’s why we craft custom waterproofing systems using advanced materials designed to stand up to San Antonio’s heat, humidity, and heavy rain. Whether your building is brand-new or decades old, we’ll tailor a solution that protects your elevator for the long haul.
Expert Installation You Can Trust
Proper waterproofing is all about the details. Our experienced technicians don’t just apply sealant and call it a day—they follow a precise, step-by-step process using proven materials and methods. Every component is installed with care to make sure it holds up under pressure. The result? A dependable waterproofing system that keeps moisture out and your elevator system safe and sound.
Ongoing Preventive Maintenance
We believe good service doesn’t end once the installation is complete. To keep your elevator pit protected year after year, we offer preventive maintenance plans tailored to your needs. Regular inspections and maintenance help identify potential issues early, providing peace of mind and preventing costly repairs in the future. This is a smart way to protect your long-term investment.
Schedule Your Elevator Pit Assessment Today!
Protecting your elevator system starts with knowing what’s going on below the surface. Schedule a detailed inspection with Elevate Enterprises, LLC, and let our experienced team take a close look at your elevator pit. We’ll spot potential trouble areas early and recommend waterproofing solutions that fit your building’s exact needs. Don’t wait for water damage to do real harm—take action now to keep your system safe and running strong.
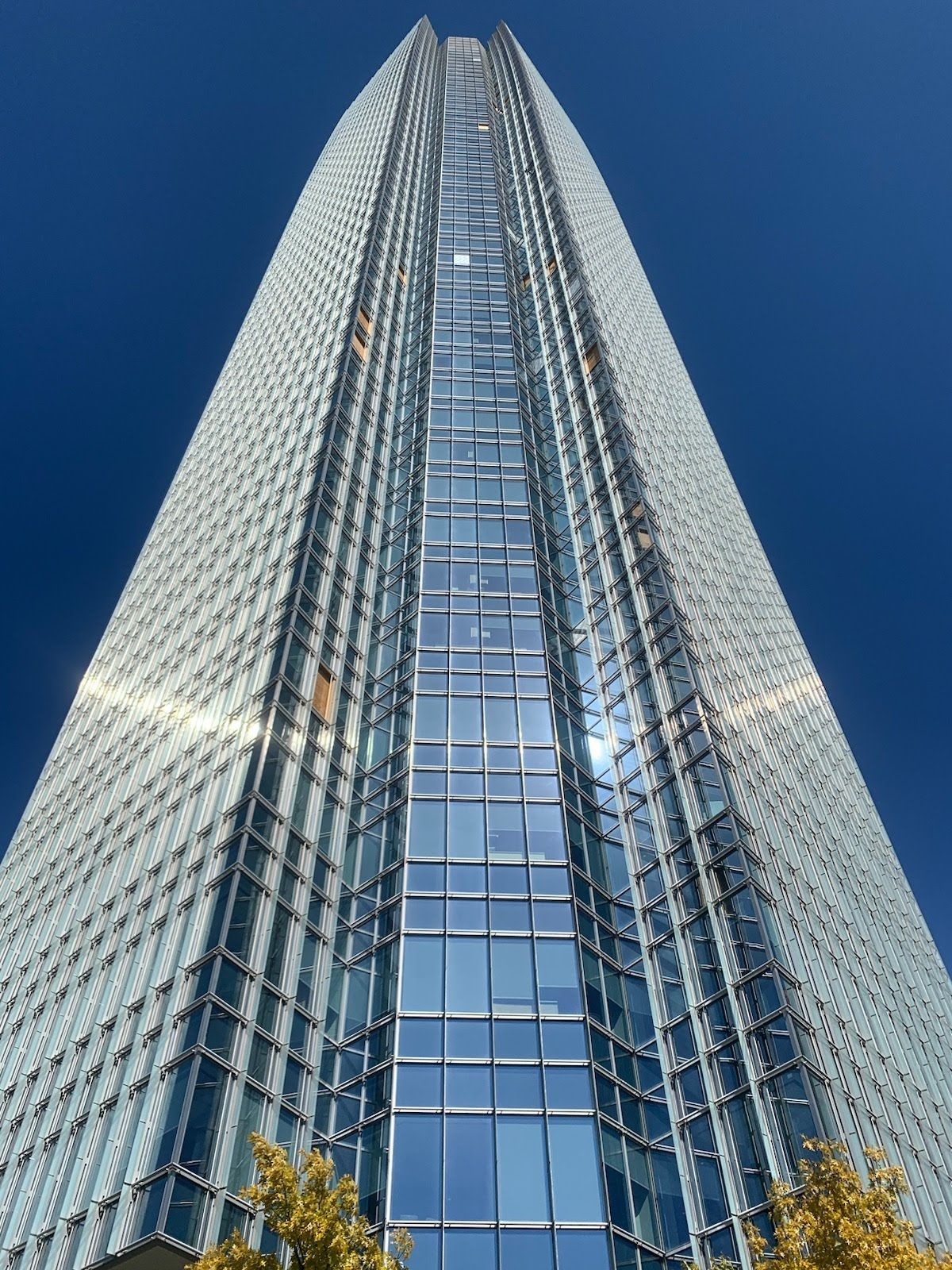
A Smarter Approach to Elevator Pit Protection
At Elevate Enterprises, LLC, we believe that effective waterproofing starts with preparation—and ends with precision. Our elevator pit waterproofing process is designed to deliver lasting results by addressing water intrusion at its source, using the highest-quality materials and a methodical, step-by-step approach.
Step 1: Surface Preparation
Before we apply any waterproofing system, we take the time to thoroughly inspect and prepare the elevator pit.
- Cleaning the entire surface to remove debris, dirt, and any contaminants
- Repairing cracks, spalls, or surface imperfections to ensure a smooth application
- Priming the area as needed for optimal adhesion
This critical first step ensures that the waterproofing membrane can bond securely and perform as intended.
Step 2: Precision Membrane Application
Once the surface is cleaned and prepped, we install a waterproofing membrane that’s made to hold up in real-world conditions. It’s not a temporary patch—it’s a durable barrier that keeps moisture out for the long haul.
We take our time to get it right, working it into every seam, corner, and hard-to-reach spot. The material stays flexible, so it won’t crack or separate as the structure settles or shifts.
No two pits are the same, which is why we don’t rely on stock solutions. We match the membrane to your site—choosing the right product to make sure the job holds up over time.
Step 3: Reinforcing with High-Quality Sealants
After the membrane is applied, we seal up the most vulnerable spots—places like pipe entries, floor-to-wall joints, and small cracks that could let water sneak through.
We use heavy-duty, industrial-grade sealants that are built to last. This extra layer helps lock down the entire system, backing up the membrane and closing off any potential weak points. It’s one more step to make sure moisture stays out—and your elevator stays protected.
Step 4: Curing for Long-Term Results
Once the membrane is in place, we let it cure fully—no shortcuts. This step is key to making sure everything bonds correctly and holds up under real-world conditions.
Proper curing helps the material lock in tight, reach its full strength, and do the job it’s meant to do. We follow manufacturer guidelines and adjust for temperature, humidity, and airflow, giving the system the time it needs to set right and last long.
Compliance with Elevator Codes and Safety Regulations
Water in an elevator shaft isn’t just a maintenance issue—it’s a code violation. Left unchecked, it can lead to safety risks, fines, and costly repairs. Our waterproofing services help keep you fully compliant with key standards, including:
- ASME A17.1 elevator safety codes
- NFPA 70 electrical requirements
- OSHA guidelines for worker safety
- ADA accessibility standards
- Local building and municipal codes
Ignoring water intrusion doesn’t just put your equipment at risk—it can create legal and operational headaches you don’t want. We help you stay ahead of the problem, and in full compliance.
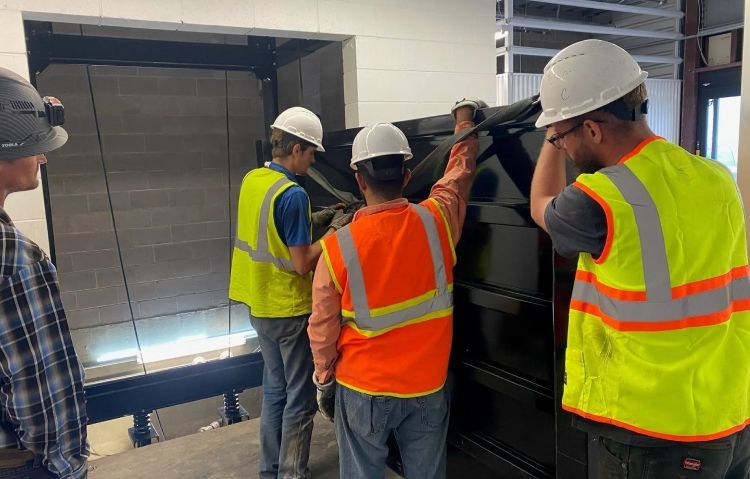
Tailored Waterproofing for Every Property Type
We offer customized solutions based on building type, usage, and environmental conditions.
Commercial Buildings
- High-traffic applications
- Multi-level shaft protection
- Minimal service interruptions
Residential Properties
- Basements with private elevators
- Protection from foundation water seepage
- Non-disruptive installation
Industrial Facilities
- Heavy-load shaft support
- Chemical and waste water resistance
- Reinforced systems for extreme conditions
The Cost of Delaying Waterproofing Services
Waiting too long to waterproof your elevator pit can cost you—both in time and money. Small leaks often lead to bigger issues, like repeated breakdowns, costly repairs, and long-term damage to your property’s value. It may even push your insurance rates higher.
Handling it early isn’t just about avoiding problems—it’s a smart investment that protects your equipment, lowers maintenance costs, and keeps things running safely for years to come.
Long-Term Maintenance and Monitoring Services
Post-installation, we offer continued support and annual maintenance packages:
- Scheduled inspections
- Moisture monitoring systems
- Reapplication of sealants as needed
- Emergency water intrusion response
Environmentally Conscious and Safe Materials
We prioritize sustainability without compromising performance:
- Low-VOC coatings
- Non-toxic polymers
- Recyclable drainage systems
Safety for building occupants, technicians, and the environment is always a top priority.
Key Takeaways: Why Waterproofing Your Elevator Pit is Essential
- Prevents corrosion and elevator failure
- Ensures legal and safety compliance
- Protects building infrastructure
- Minimizes long-term costs
- Enhances property marketability
Frequently Asked Questions
How Often Should Elevator Pit Waterproofing Be Done?
It depends on factors like your building’s age, location, and prior maintenance. In general, we recommend inspecting your elevator pit annually and reapplying waterproofing every 3 to 5 years. Regular maintenance helps prevent serious issues and keeps your system protected from long-term damage caused by moisture or water intrusion.
Is Elevator Pit Waterproofing Necessary in San Antonio, TX?
Definitely. San Antonio’s mix of heavy rainstorms and high humidity can take a toll on elevator pits. Without waterproofing, moisture can seep in and cause rust, electrical issues, and mold. Waterproofing isn’t just a good idea—it’s a smart investment in your building’s safety and your elevator’s long-term performance.
Can Elevator Pit Waterproofing Be Done in an Existing Building?
Yes, absolutely. You don’t need a new construction to benefit from waterproofing. We specialize in retrofitting existing buildings with custom waterproofing solutions. Our team carefully inspects your elevator pit, then applies systems that fit your current structure—no major renovation required, just dependable protection against future water damage.
Secure Your Elevator Pit with Professional Waterproofing
Water intrusion is not just an inconvenience—it’s a structural and safety threat. Our expert waterproofing services deliver reliable, code-compliant protection that endures. Don’t wait until costly repairs or safety violations occur.
Call now or request a consultation to protect your property’s elevator system with professional waterproofing solutions. Let’s build your defense against water damage—before it starts.
- Free on-site evaluations
- Fast turnaround
- Certified and insured professionals
- 100% satisfaction guarantee